Source: Images and content by A JOYFUL EXPRESSION OF THE ART DECO SPIRIT OF REVERSO @ Jaeger LeCoultre.
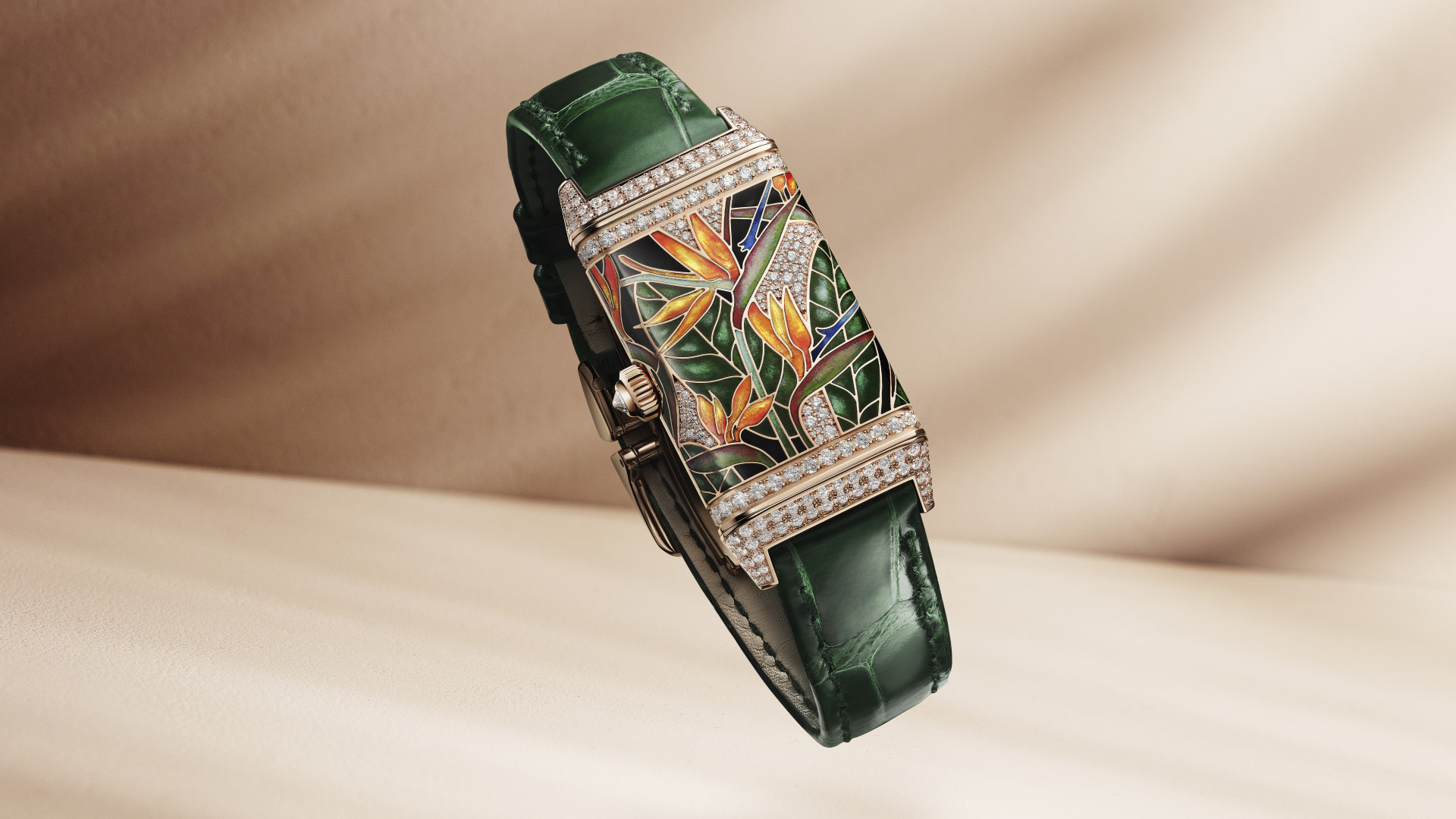
A complex dance of artistry and craft to create objects of rare beauty
The restrained elegance of the Reverso One dial design is a perfect foil for the rich and colourful decoration of the cases: on a background of white mother-of-pearl, gold brackets define the four corners of the dial, creating a frame within which the numerals, in the signature Reverso One font, are set. Grain-set diamonds decorate the gadroons and lugs and the winding crown is adorned with a reverse-set diamond.
The new designs give full rein to the artistry and diverse skills of the Métiers Rares™ atelier, with several artisans collaborating in a carefully orchestrated process over the course of many weeks and months. The floral designs wrap seamlessly around the case-sides, from the back to the bezel, involving curves and angles that add a high degree of complexity to the artisans’ work.
Champlevé (which literally means ‘raised field’) is one of the oldest decorative enamelling techniques. To begin with, sections of the flat metal surface of the case are hollowed out to leave an outline of the desired motif. The enameller then begins painting the details and tonal nuances of the design into the remaining wells and troughs with enamel, one layer at a time – in varying combinations of transparent and opaque enamels to achieve the desired effect. Research into the colours – a long process of trial and error because of the way that enamel pigments react at high temperatures – took more than 50 hours, before the work could even begin.
These new ‘Precious Flowers’ designs further elevate the craft of enamelling by combining it with paillonnage. Tiny pieces of 24-carat gold leaf are cut to the exact shape and size of the pattern to be filled in. After a clear layer of fondant enamel has been completed, the enameller takes these tiny fragments and fixes them into place, modelling them to fit the desired space perfectly. Only then can the process of working with the coloured enamel begin.
The cases require 10 or more firings, each one building the intensity and depth of colour. Grand Feu enamelling requires many years of experience as well as great technical skill because the outcome is unpredictable: firing at temperatures up to 800º Centigrade changes the chemistry of some pigments and only with many years of experience can an enameller predict whether the final colours will be as desired. While every firing increases the beauty of the piece it also increases the risk: the enamel may bubble or crack; it may burn and shrink; or the metal base may warp.
On designs with diamond-set backgrounds, the gem-setting can begin only after the enamel work is completed, adding to the delicacy and complexity of the task. Indeed, combining enamelling and gem-setting is a delicate dance between the artisans: while firing hardens the gold, the gem-setter requires soft metal, so the challenge is to find the ideal balance.
At any point during enamelling or gem-setting, the slightest mistake could destroy countless hours of work. These are process that cannot be rushed and that is what makes these decorative crafts so intriguing, going a long way to explaining why they are so highly prized.